1. 系统概述
公司在数年研究国内外各种DCS产品的技术基础上,结合多年在发电、冶金、石化等生产过程的控制经验推出了工业锅炉的分散控制系统(DCS),是一个融计算机、网络、数据库和现代自动控制技术为一体的工业信息技术品。
2. 系统组成
* 本系统采用先进的PLC+分布式IO+现场总线组成的控制系统,具有可靠性高、易维护、停炉检修损失小的特点,设计有手动、自动、故障报警保护功能。
*上位计算机系统硬件部分采用工控机,采用美国GE、德国西门子组态软件进行组态。
* 锅炉部分的控制系统采用西门子、施耐德、AB、美国GE先进的可编程控制器PLC ,通过PLC通讯接口与上位工控机相连。
*数据采集采用先进的分布式IO采集控制系统,锅炉房控制模块与配电间控制模块间通过现场总线相连,传输速率快,设备动作迅速。
*采用先进的闭环控制模块对锅炉压力、汽包水位、过热蒸汽温度、燃烧进行闭环调节,以确保锅炉运行稳定。
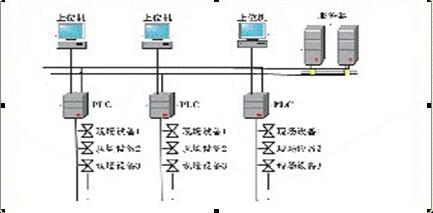
3. 系统特点
安全可靠:多重完善的联锁保护功能确保锅炉安全运行
质量优秀:在相同条件下选用尽可能可靠的仪表电气元件,提高电控柜的质量,降低售后服务成本;降低锅炉厂锅炉质保金的收款风险;减少用户因电控柜问题停炉而造成巨大生产损失单实用:符合中国国情(中国工厂的司炉工和维修电工无法应对复杂电控柜的使用维修),简单实用的设计可有效避免用户因操作不当和无法维修造成停炉损失维修成本低:采用标准通用的电器元件,便于采购维修,节约采购维修时间和成本,减少停炉损失后备手动:当系统中某部分出现故障无法进行自动控制时,检修期间,在司炉工实时监视下可进行后备人工手动操作,减少用户因停炉而造成的生产损失。
4. 系统功能
4.1监控功能
系统在运行过程中,上位机将下位机采集上来的锅炉运行数据进行实时处理,通过上位机的分析,判断,实现对现场温度、压力、液位、流量等工艺过程参数的模拟动态显示,通过下位机的反馈至上位机的信号实现对现场仪表、风机、水泵及燃气调节阀系统运行状态的监控。现场通过上位机手动和自动切换,实现风机,水泵的启、停控制。系统与现场仪表,电气设备配合可实现多变量闭调节(如送风门调节、引风门调节)和联锁控制,以保护整个锅炉的正常运行。
4.2报警功能
系统具有故障报警(风机、水泵、上煤系统等的启、停故障等)和超限报警(高、低液位、压力、流量、温度报警及用户指定的其它参数报警),能够以声光报警的形式提醒锅炉运行人员及时的发现并处理报警原因。
4.3数据报表记录功能
可根据用户的要求,对锅炉流量、温度、压力、炉膛负压等工艺参数及电机负载情况等数据进行及时的记录备份,以备以后调出查询。
4.4数据查询及报表打印
计划,打印功能,用户对记录的报表数据,报警数据进行查询、打印。
4.5曲线功能
对用户关心的温度、流量等信号,系统以实时、历史趋势曲线的形式直观地表示出来,能够通过多种方式进行统计查询,方便用户操作。
4.6密码保护功能
为防止非专业人员随意改动参数,造成对锅炉操作的误动作,该系统可配制几个操作员密码,操作员可以键入唯一的标识符和口令进入较高级的系统修改参数。
4.7模拟仪表操作盘:
系统设有模拟仪表盘,操作人员输入正确密码后可以方便地设定各项系统参数,就仿佛在仪表盘上操作一样,操作简单、便于理解。
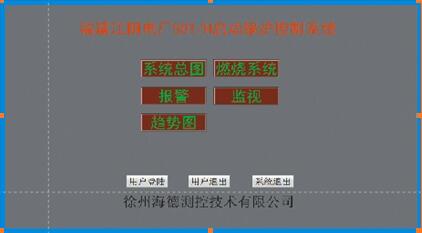
启动画面
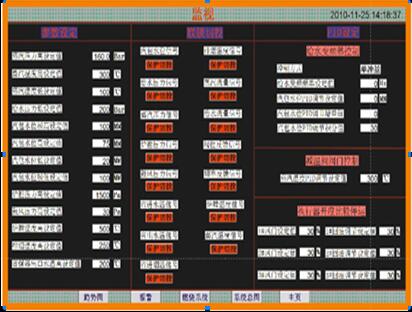
监视
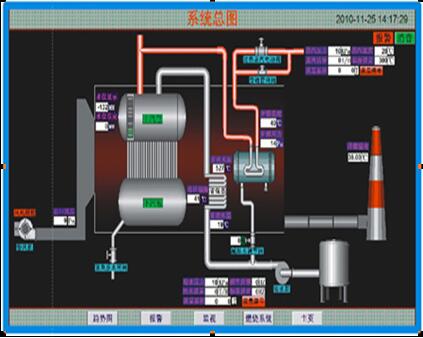
系统图
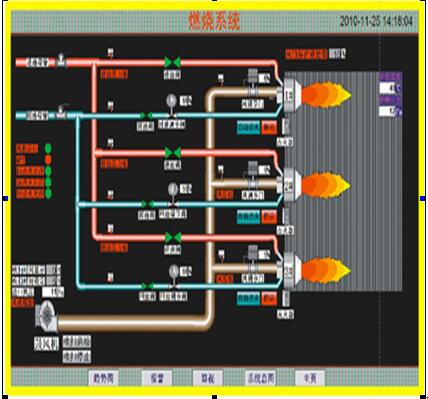
燃烧系统